
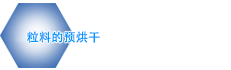
1. Glamide®通常以干粒料的状态装入防潮袋中发货,如果开封后马上成型,则不需要预烘干。
2. 但是,如果以开封后的状态持续放置,粒料便会吸湿,因此请避免长时间放置。
3. 吸湿后的粒料的一般干燥条件为80~120℃烘干3~5小时。但是,如果长时间烘干,容易因氧化产生变色,请注意。
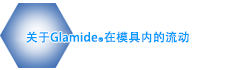
在“流动”的阶段,树脂的前端(压力为零)被后端(有压力)推动前进。与模具表面接触的“皮肤层”冷却凝固,但内部的“核心层”在未冷却的状态下继续流动。皮肤层的正下方产生流动阻力,该阻力被视为剪切应力,剪切应力/剪切速度被视为粘度。一般流体的粘度是一定的,但塑料的粘度却随着剪切速度的变化出现很大的差异。这便是塑料具有的独特而复杂的流动性质,聚酰胺树脂在剪切速度变大时,粘度下降。一旦注塑速度加快,流动性就变好。

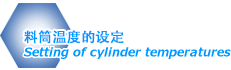
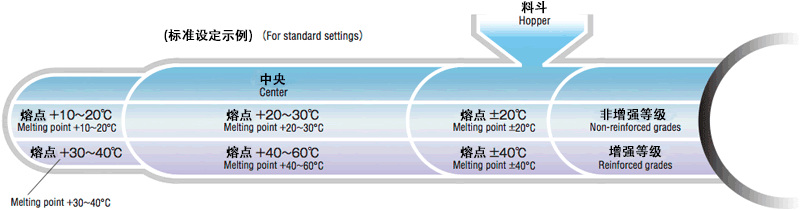
(注)
关于实际上树脂的清洗温度,普通聚酰胺请设定为300°C以下,6T聚酰胺请设定为330°C以下。若高于此温度,会发生热分解,引起老化,并引起燃气、色调不良等问题。
关于实际上树脂的清洗温度,普通聚酰胺请设定为300°C以下,6T聚酰胺请设定为330°C以下。若高于此温度,会发生热分解,引起老化,并引起燃气、色调不良等问题。
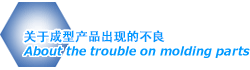
不良 | 原因 |
---|---|
尺寸不均匀 | 1. 热嘴供给不均匀。 |
2. 料筒加热温度有很大波动。 |
|
3. 孔穴数太多,流道系统太复杂。 | |
4. 浇口不均匀。 | |
5. 重新利用的聚合物和新的聚合物没有混合均匀。 |
|
6. 料斗内的热嘴受到不均匀加热。 | |
7. 周期不当。 | |
8. 模具紧固力或者注塑压力不当。 | |
毛边 浇口中心有线状纹路 |
1. 热嘴吸湿。 |
2. 聚合物的加热。 | |
3. 加入添加剂,添加剂的沸点太低。 | |
熔接痕 | 1. 排气不充分。 |
2. 模具温度太低。 | |
3. 注塑压力太低。 | |
4. 注塑速度太慢 | |
银条 | 流动时的剪切所引起,要加大浇口口径。或者通过调整树脂温度、填充速度,创造剪切力小的良好成型条件。 |
2. 冷料井的加强。 | |
困气烧焦 | 1. 聚合物的加热。 |
2. 注塑速度太快。 | |
3. 排气不充分。 | |
“凹陷”及表面的“缩痕” | 1. 浇口太长,或者太小。 |
2. 聚合物的加热。 | |
3. 因注塑压力损失引起的反作用。 | |
4. 注塑压力太小。 | |
5. 唧嘴或者流道太小。 | |
6. 螺杆前进的时间太短。 | |
7. 注塑速度太快。 | |
着色 | 1. 聚合物的加热。 |
热嘴的干燥时间太长,或者干燥温度太高引起的氧化。 |
|
3. 产品成型前的料筒内的着色聚合物去除不充分。 | |
挤出困难 | 1. 周期太短。 |
2. 聚合物温度太高。 | |
3. 挤出系统设计不当。 | |
4. 脱模角度不当。 | |
5. 浇口太长,或者太小。 | |
6. 聚合物的加热。 | |
坚韧性不足 | 1. 热嘴吸湿,或者聚合物的加热。 |
2. 浇口位置不当。 | |
3. 孔穴内聚合物流动的角度太细。 | |
4. 填充剂、颜料引起的污损或者添加量过多。 | |
5. 树脂温度低,或者含有未熔融的聚酰胺。 |
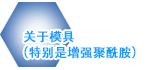
(1)模具材质
一般加入玻璃纤维等填充材料的增强聚酰胺比非增强聚酰胺在成型过程中的模具磨损较大,因此请注意以下几点。特别是浇口部位,请选择以下的模具材质。
- 将SK、SKS、SKD等合金工具钢进行淬火回火处理,作为HRC55~60使用。
- 使用预硬钢、沉淀硬化钢。
- 进行表面硬化处理。
- 镀硬铬处理
- 氮化处理
- 金属陶瓷处理
(2)浇口
设计浇口时,必须注意避免玻璃纤维的切损。玻璃纤维增强聚酰胺比非增强聚酰胺的流动性差,因此特别重要的是需在流道和浇口的接口部位拐角处充分倒R角,以减少流动阻力。另外,请充分考虑因浇口位置的不同,可能会使熔接痕明显,或者出现强度下降、变形等问题。关于浇口的尺寸,通常侧浇口的厚度是成型产品厚度的约60%,宽度是浇口厚度的1.5~3倍,流道长度是浇口厚度的约50%。针孔型浇口则以0.8~1.5φ为标准。
(3)通风孔
增强聚酰胺与非增强聚酰胺相比,更容易产生气体,因此在树脂流聚集的地方,尽可能安装深度为50μm左右的通风孔,使气体易于排出。
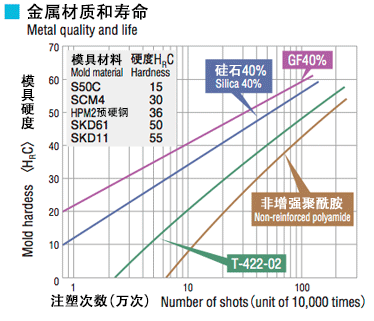