
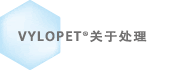
成型条件的选择
预烘干
即使很少的水分也会导致热塑性聚酯树脂在成型过程中因加水分解等发生起泡、滴垂、外观不良,而且还会引发物性降低。为了保证成型稳定性和成型品的品质,请务必实施预烘干。此外,如果将已烘干的颗粒放置在空气中的话就会吸水,因此如果放置时间超过30分钟,请再次烘干后使用。
烘干条件的标准(120℃不适宜)
树脂温度 | 烘干时间 |
130℃ | 4〜6小时 |
140℃ | 3〜5小时 |
成型前务必要对VYLOPET实施预烘干。
请设置烘干条件,确保颗粒含水率不高于0.025%(最好不高于0.020%)。
请设置烘干条件,确保颗粒含水率不高于0.025%(最好不高于0.020%)。
能够用加料斗干燥器和带进出料架的烘干机来实施预烘干。尤其建议使用除湿类型的烘干机。烘干条件会因烘干机的类型和烘干量而存在一些差异,请确认颗粒温度等。
尤其是重视气体的成型品,请将烘干时间设置得稍长一些,尽量降低含水率。
尤其是重视气体的成型品,请将烘干时间设置得稍长一些,尽量降低含水率。
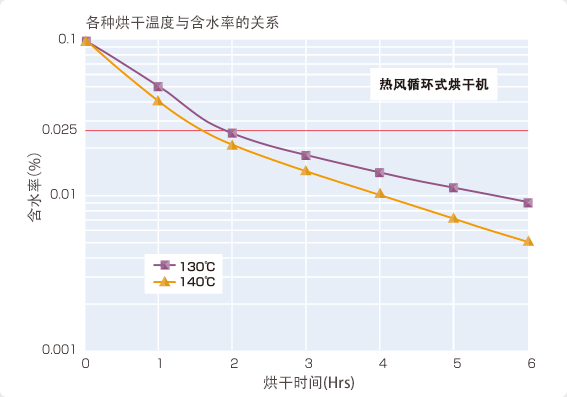
成型条件
气缸温度
右边显示的是气缸的建议温度范围(不包括加料斗下)。由于阻燃剂对热不稳定,因此请考虑尽可能将气缸温度设置得低些。
气缸温度
PET系 | 265〜285℃ |
PET/PBT系 | 260〜280℃ |
PBT系 | 240〜260℃ |
滞留时间
如果使VYLOPET在气缸内长时间滞留,就会导致热老化,机械强度降低、流动性发生变化或发生变色。如果滞留时间超过10分钟,请注射几次,实施吹扫,并在清除气缸内的滞留部分后,重新开始成型。
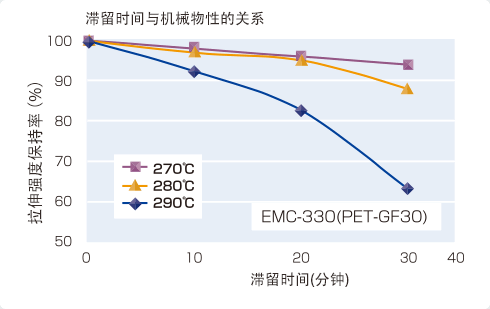
模具温度
请研讨并设置成型品的尺寸和翘曲、外观、成型周期。如果PET系的模具温度达到85〜120℃,并且重视外观,建议设置为120℃以上(〜135℃)。此外,虽然模具温度达到40〜70℃就能够成型,但是二次收缩将变大。PBT系、PET/PBT系的标准温度是50〜70℃,如果重视外观,建议设定为80〜100℃。
射出速度
为了获得良好的VYLOPET外观,射出速度越快,越能够获得表面光泽良好的成型品。但是,如果射出速度较快,就存在成型品翘曲和烧焦的风险,请根据成型品的外观来判断并设置。
成型条件的选择
模具材质
关于模具,建议采用具有卓越的耐磨损性的高合金钢。GF强化系采用SKD-11是最普通的,此外,也使用SKD-61和SUS420、SUS440系的不锈钢钢材。无论上述任意一种材质,与R55相比,最好使用淬火、回火处理后HRC(硬度)达到R60左右的钢材。对于阻燃GF强化系,如果使用耐腐蚀性良好的SUS310和SUS440系,则具有提升模具的耐久性的效果。
模具温度调节
模具的温度调节通常使用筒形加热器、温水或油温调节。由于模具温度对成型周期和成型品的外观及品质等具有较大的影响,请充分考虑模具温度分布、流量和型芯冷却等。为了保持模具温度的均匀性,如果在模具与模板之间使用隔热板,则更加有效。
流道与注道
一般情况下,采用截面呈圆形或者梯形横截面的流道。请不要使用半圆形和矩形横截面。此外,请务必在流道及注道的前端设置冷料穴。
出模角
虽然出模角的大小取决于模具的研磨精度和材料的成型收缩率,但是一般情况下,有必要确保0.4〜1度的出模角。
气孔
由于需要考虑防止发生成型品烧焦、成型品外观、熔接线强度下降等,因此需务必设置适当的气孔。气孔的深度至少要达到0.02〜0.05mm,尽可能设置更大的宽度,在距离模腔0.75mm左右的位置,将气孔深度设置为3mm左右,并延伸至模具的边缘,再实施气孔排气。
成型不良的原因与对策
不良现象 | 原因 | 对策 | |
凹陷 | 成型条件 | 1.成型温度较高 2.模具温度较高/较低 3.射出的保压较低 4.射出的保压时间较短 5.冷却时间不足 6.没有垫料 |
1. 调低气缸温度 2. 适当设置模具温度 3. 调高保压 4. 增长保压时间 5. 增长冷却时间 6. 确保垫料量达到5〜10mm |
设计 | 1.流道、浇口较小 2.浇口位置适当 |
1. 扩大流道、浇口 2. 在加工余量部位设置浇口 |
|
成型机 | 1.射出时发生了逆流 | 1. 检查及更换逆流防止阀 2. 增长保压时间 3. 增长冷却时间 4. 另行控制型腔和型芯的温度调节 |
|
翘曲 变形 |
成型条件 | 1.射出条件不适当 2.保压时间较短 3.冷却时间较短 4.型腔和型芯的温度差距较大 |
1. 调高射出压力及速度 |
模具 | 1.成型品的脱模不平衡 2.脱模销的面积较小 |
1. 让脱模更加平衡 2. 扩大脱模销的面积。 |
|
设计 | 1.浇口位置不适当 3.产品尺寸较大, |
1. 变更浇口位置 2. 变更形状,确保加工余量变动更加均匀 3.设置多点浇口 |
|
毛刺 | 成型条件 | 1.树脂温度较高 2.射出速度较快 3.保压较高 4.合模压力较低 5.树脂的填充量较多 |
1. 调低气缸温度 2. 调整射出速度 3. 适当保压 4. 调高合模压力 5. 设置5mm左右的垫料量 |
模具 | 1.模具的模面不平滑 | 1.实施模具的修正 | |
烧焦 | 成型条件 | 1.树脂温度较高 3.射出速度较快 |
1. 调低气缸温度 2. 调低螺杆机转速 调高背压 3. 调低射出速度 4. 缩短成型周期 适当设置成型机尺寸 |
模具 | 1.排气不充分 | 1.增加气孔 | |
设计 | 1.浇口位置不适当 2.浇口尺寸较小 |
1. 变更浇口位置, 确保焊接线进入分型面 2. 扩大浇口尺寸 |
|
熔接线 | 成型条件 | 1.树脂温度较低 2.射出压力/速度较低 3.模具温度较低 |
1. 调高气缸温度 2. 调高射出压力/速度 3. 调高模具温度 |
模具 | 1.排气不充分 | 1.增加气孔 变更浇口位置, 确保焊接线进入分型面 |
|
光泽 | 成型条件 | 1.树脂温度较低 2.模具温度较低 3.射出速度较低 4.保压不充分 5.树脂的填充量较少 |
1. 调高气缸温度 2. 调高模具温度 3. 调高射出速度 4. 调高保压时间 5. 设置5〜10mm的垫料量 |
模具 | 1.排气不充分 2.模具很脏 |
1. 增加气孔 2. 清洗模具 |